Introduction
Optotune uses electroactive polymers (EAPs) as an electrostatic actuator for its series of laser speckle reducers. These so-called "artificial muscles" can undergo a large amount of deformation while sustaining large forces. While today's piezoelectric actuators only deform by a fraction of a percent, EAPs can exhibit a strain of up to 380%. There are different types of EAPs. Optotune has specialized in dielectric electroactive polymers (DEAPs) as described below. A detailed discussion on all types of EAPs can be found here.
Dielectric electroactive polymer principle
DEAPs are driven by an electric field: when a voltage V is applied between two compliant electrodes that sandwich a dielectric elastomer, an electromechanical thickness strain
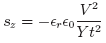
is induced by electrostatic forces (Maxwell’s stress). Here, t is the thickness of the dielectric elastomer, Y represents the modulus of elasticity, ε0 denotes the permittivity of free space and εr is the dielectric constant of the elastomer (typically about 3). Using the constant volume approximation (1 + sx)(1 + sy)(1 + sz) = 1 (Poisson’s ratio = 0.5) and assuming that the thickness compression results in an equi-bi-axial planar strain (splanar = sx = sy), we obtain
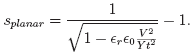
Advantages
DEAPs have many advantages compared to piezoelectric actuators, voice coils or motors:
- Large deformation: While a strain of up to 380% has been reached in experiments, the commercially viable DEAPs are in the range of 20%.
- High energy efficiency due to the purely electrostatic principle
- Moderate bandwidths of a few kilohertz achievable
- Large operating temperature range of -100°C to 250°C
- Low noise and vibration
A downside is the high voltage required. While DEAPs are typically driven at > 1 kV, Optotune has optimized materials and processes to reach about 15% deformation at 300V.
Applications
Optotune has specialized in the use of electroactive polymers as an actuator in optical components such as laser speckle reducers, tunable diffraction gratings or tunable phase retarders. The DEAP principle can also be used as sensor or even as a generator. Application examples include electroactive fluid pumps and valves, spring roll actuators in robots, heel-strike generators, a blimp and ultraflat loudspeakers.
Videos
The video below shows an EAP pulsed with 300 volts (download avi-file)
Further reading
Electrostriction of polymer dielectrics with compliant electrodes as a means of actuation
R. Pelrine, R. D. Kornbluh, and J. P. Joseph, Sens. Act. A: Physical, 64(1): 77-85 (1998).
High-Speed Electrically Actuated Elastomers with Strain Greater Than 100%
R. Pelrine, R. Kornbluh, Q. Pei, and J. Joseph, Science, 287:836-839 (2000).
Polymer artificial muscles
T. Mirfakhrain, J. D. W. Madden, and R. H. Baughman, Materials Today, 10(4):30-38 (2007).